We use cookies and other tracking technologies to improve your browsing experience on our website, By clicking "Accept All," you agree to allow cookies to be placed to enhance your browsing experience on this website to show you personalized content and targeted ads, to analyze our website traffic, and to understand where our visitors are coming from. You can manage your cookie settings below. Clicking "Confirm" indicates your agreement to adopt the current settings.
How to Save Costs while Increasing Production Yield for Narrow-width Films and Bags
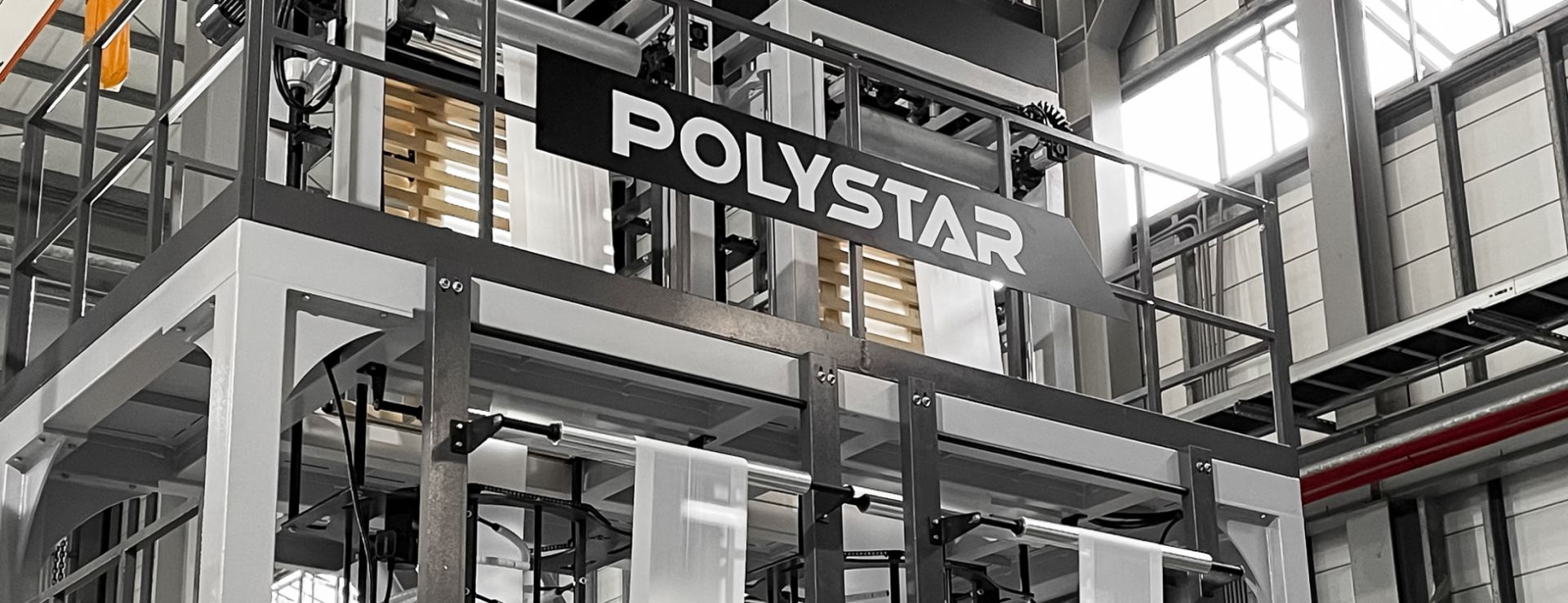
Producing narrow-width film and bags may be challenging in terms of profitability. You need to reach a certain production capacity to surpass the break-even point to make a profit, where you should control several costs, time, labor, and factory space.
It might sound challenging, but we have some good news for you. POLYSTAR provides several effective solutions to overcome this challenge.
Let's find out which solutions below fit you better!
1. Using A Mini Blown Film Machine for Narrow-Width Film and Bags
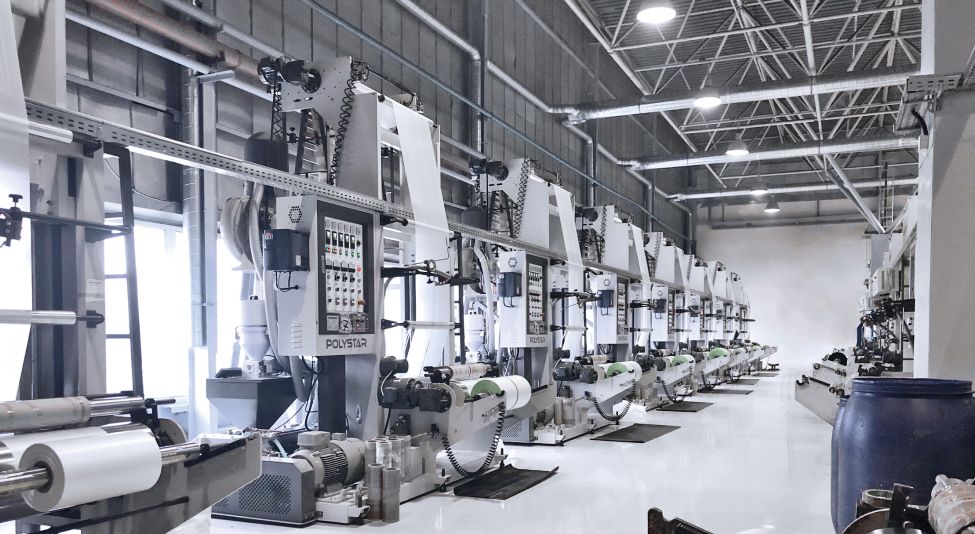
2. Twin-Head Blown Film Machine for Different-Width Tube Films at the Same Time
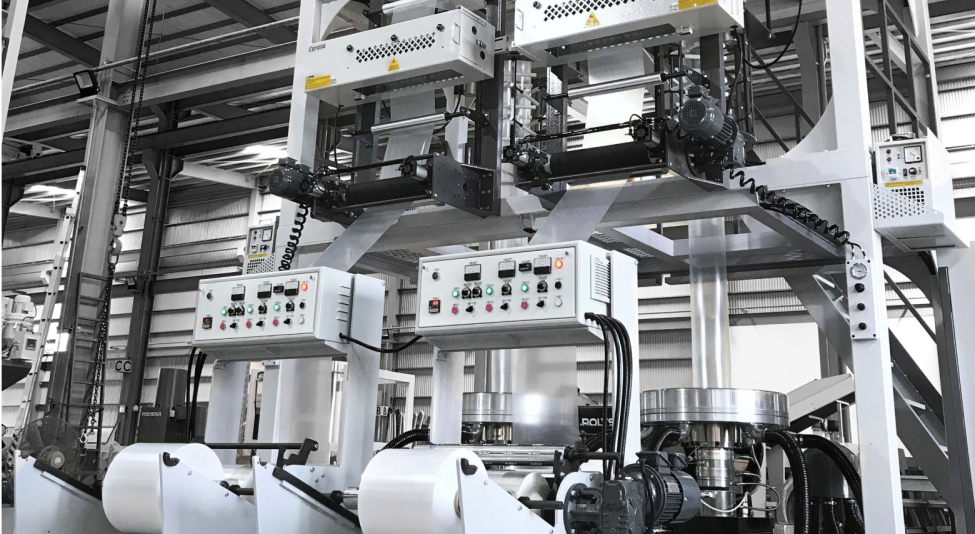
3. One Blown Film Machine for Different-Width Film Sheets at the Same Time
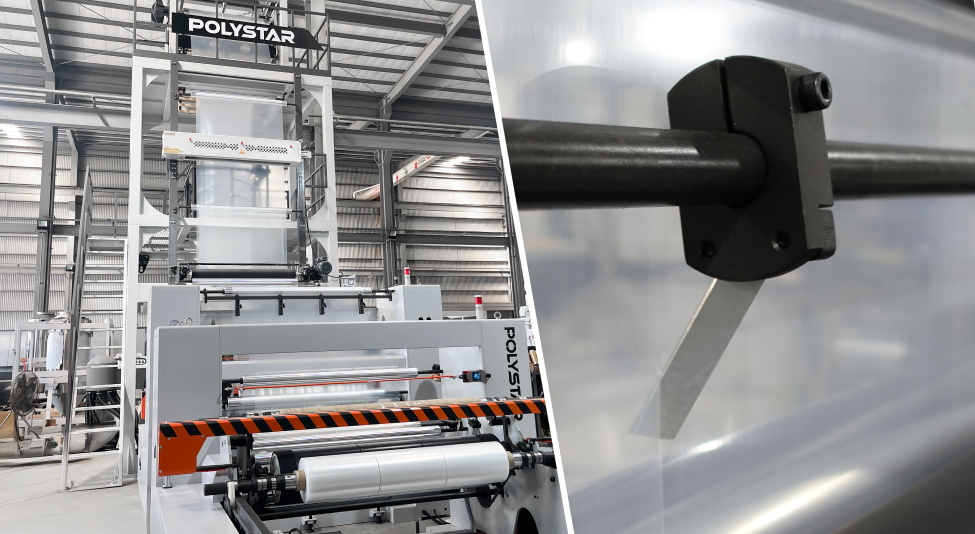
When it comes to producing sheet films, flexibility for different widths while maintaining the yield is crucial. Producing wider plastic film sheets and slitting them into narrow sheets via cold slitting knives before winding is a clever strategy.
In this way, producers do not need to use a slitter rewinder after the production. Instead, they can just slit the films during the blown film extrusion process, maximize output and achieve a more flexible production range just by changing the position of cold slitting knives.
4. Using Recycled Plastic to Reduce Material Cost in Blown Film Production
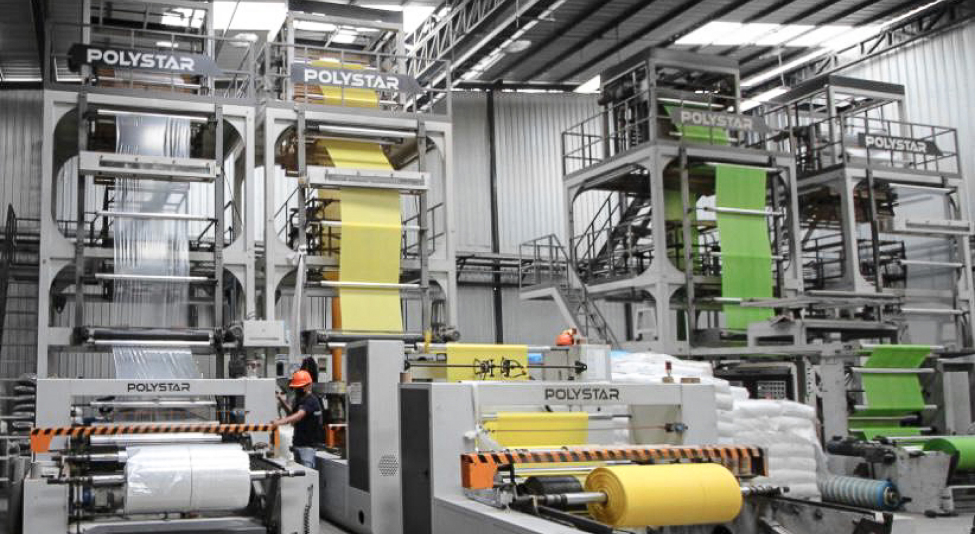
About the Author
Resul Gökpınar
International SalesResul creates up-to-date content based on his experience, gained by solving customers' problems in Turkey and the EMEA market.