We use cookies and other tracking technologies to improve your browsing experience on our website, By clicking "Accept All," you agree to allow cookies to be placed to enhance your browsing experience on this website to show you personalized content and targeted ads, to analyze our website traffic, and to understand where our visitors are coming from. You can manage your cookie settings below. Clicking "Confirm" indicates your agreement to adopt the current settings.
Agricultural Film Recycling
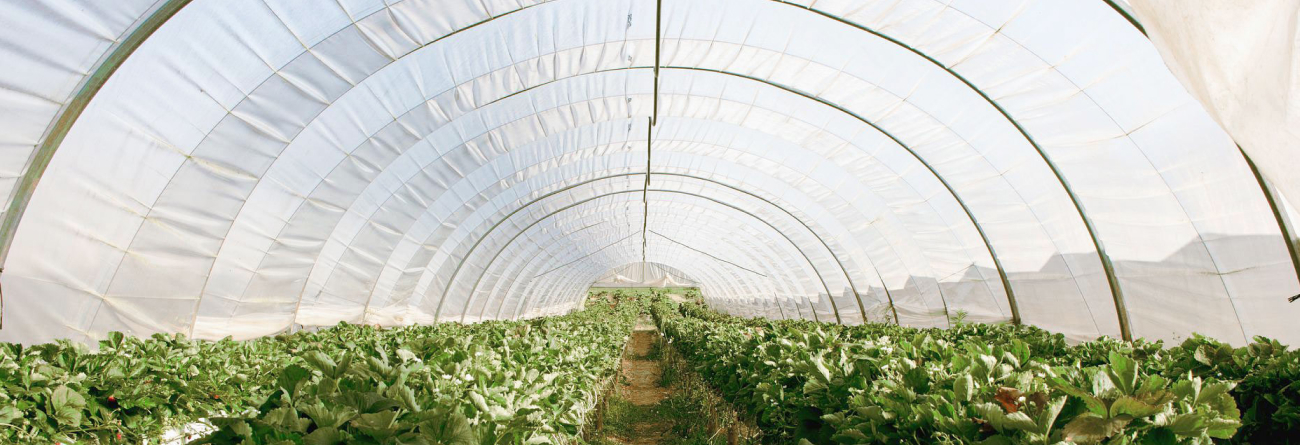
Agricultural films have become more popular as the agricultural industry continues to expand around the world. Therefore, agricultural film recycling is getting more and more important for a sustainable environment and economy.
What is agricultural film?
- Mulch Film
- Green House Film
- Banana Film
- Tunnel Film
As a result, agricultural waste is excessive and difficult to recycle. Because the properties of these plastic films are difficult to handle, they are not as simple as food plastic packaging.
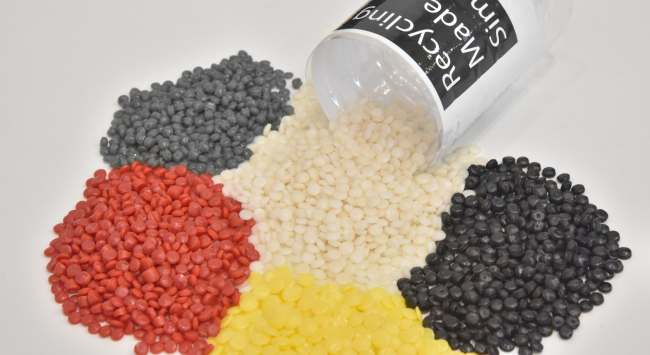
The following are the most prevalent components:
- High-density polyethylene (HDPE)
- Low-density polyethylene (LDPE)
- Additives - Polypropylene
- Insecticides
- Among other things
How to recycle agricultural film in 3 steps
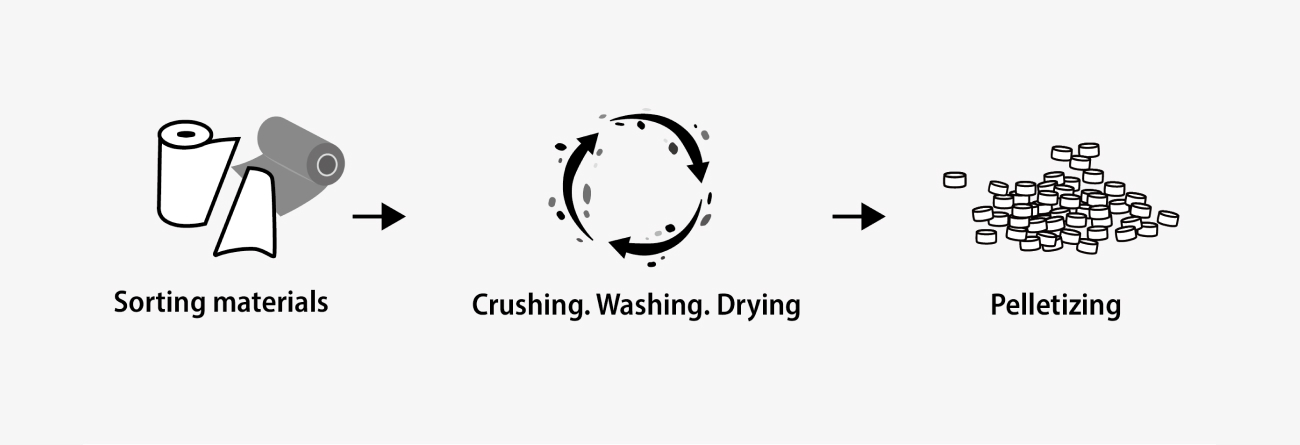
-
Sorting plastic waste materials
In agricultural applications, plastics must first be divided into the three most common types of polymers (LDPE, HDPE, and PP).
-
Crushing, washing, and drying plastic waste
It is recommended that agricultural film waste have humidity during the crushing stage since the blades of the shredders or crushers might damage the material and agglomerate the contaminants that they contain. They will next be washed on a washing line to reduce the amount of dust and sediments from the land. Normally, these washing lines require a triple washing cycle with a drying centrifuge at the end of each cycle. A hot air centrifuge is required at the end of these cycles to reduce humidity to 3 to 5%, allowing the material to be processed in a pelletizer.
-
Pelletizing plastic materials
Agricultural film wastes that have been crushed, washed, and dried are ready to go through the pelletizer extruder.
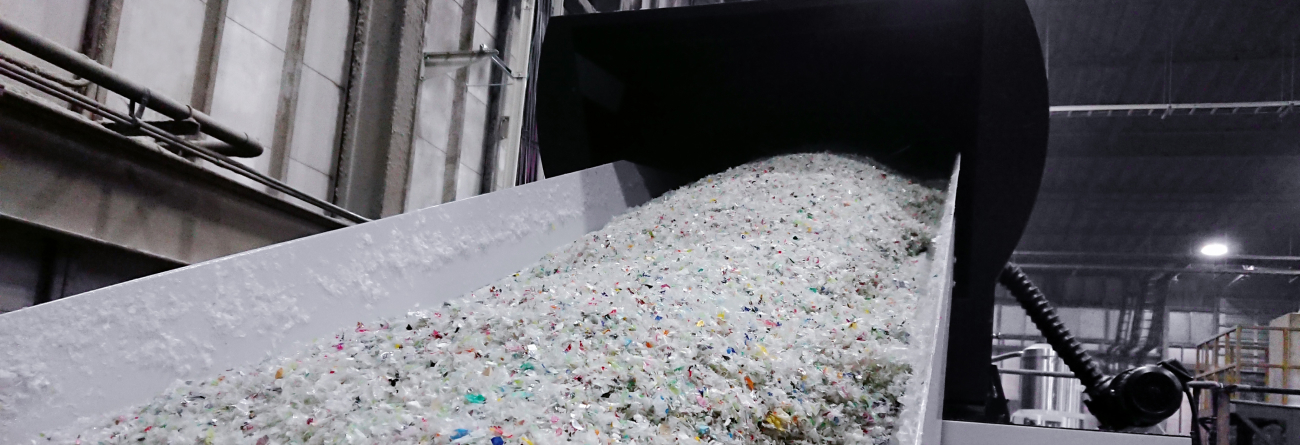
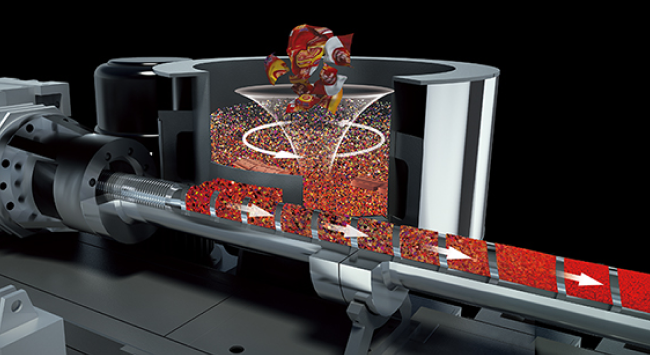

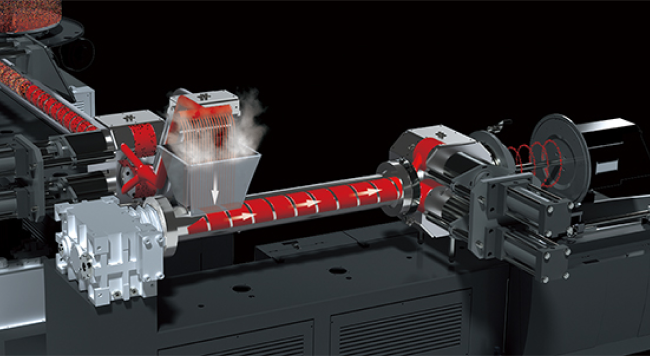
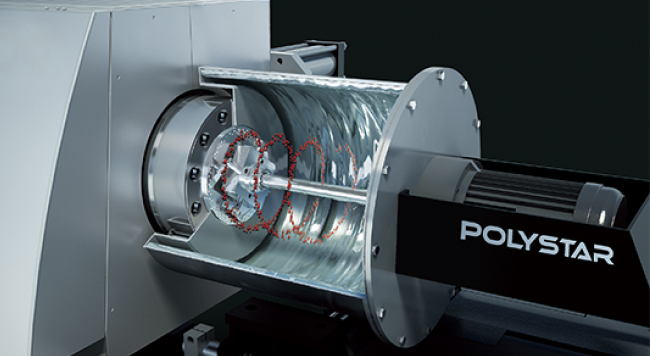
It then proceeds to the second extrusion, where it will pass a second filtration before being pelletized, to ensure that the material is prepared correctly and filtered for pelletization.
Finally, we have the pelletizing system, which homogenizes the material into pellets. After the pelletizing system, the recycled pellets pass through a water tank for cooling, then via a vibration tank to reduce the water in the cooling unit, and finally through a centrifugal dryer to entirely remove the water from the cooling unit for better drying.
About the Author
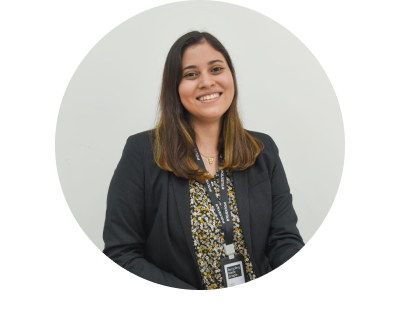
Maria Lopez
Marketing ManagerMaria Lopez is a content marketer at POLYSTAR. She authors in-depth guides that provide solutions to Plastic Producers. Not only to select your machine but also to keep you updated with the new trends.