We use cookies and other tracking technologies to improve your browsing experience on our website, By clicking "Accept All," you agree to allow cookies to be placed to enhance your browsing experience on this website to show you personalized content and targeted ads, to analyze our website traffic, and to understand where our visitors are coming from. You can manage your cookie settings below. Clicking "Confirm" indicates your agreement to adopt the current settings.
Upgrading Film Recycling Process in Chile And Ecuador
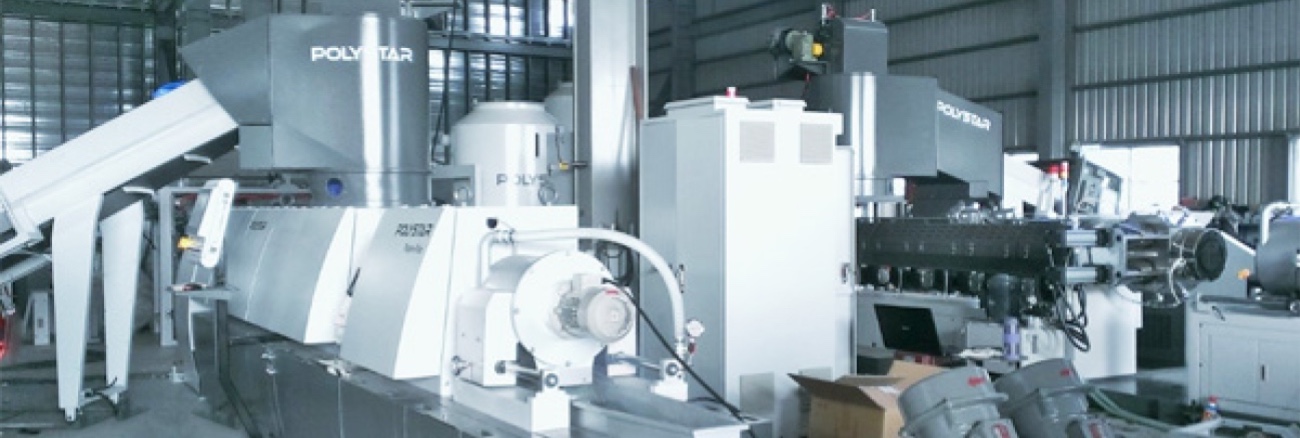
The crusher normally generates a lot of noise during the process, and the transport of material from the crusher into the extruder is problematic sometimes, because the film flakes are very light in weight, and from time to time it creates very inconsistent feeding from the hopper into the extruder, as the low bulk density of the material can make high output difficult to achieve. Normally, one can reach about 250kg per hour with a two-stage extruder of 100mm in screw diameter.
POLYSTAR's Plastic Recycling System and its Advantages
-
1. An Integrated system without the need for pre-crushing:
The integration of the cutter compactor directly with the extruder eliminates the need for pre-crushing plastic film. The feeding is therefore much faster and more stable. High throughput with the light-weighted film flakes can be easily achieved by going through the densification and compacting process first. -
2. High productivity
A 100mm screw (single stage) can achieve more than 400kg in post-industrial LDPE, whereas in the conventional line, a producer can hardly achieve 300kg. -
3. High automation with flexible waste-feeding methods:
The plastic recycling system can process scrap material on a conveyor and film-on-roll on a nip-roll film feeder simultaneously. This automates the entire process and is beneficial for producers in terms of labor cost-saving, space-saving, and lowering energy consumption. The machine generates very low noise as it does not require a separate crusher to process the film waste in advance. -
4. Lower operation cost (less space, lower energy consumption, and lower labor cost):
POLYSTAR's plastic recycling systems can process heavily printed PE/PP film in just one single extrusion stage. This replaces the traditional "two-stage" mother-baby extruder pelletizer with less material degradation, as the extrusion process is done in a single stage. At the same time, the machine consumes less energy and takes up less space because of its compactness (requires one extruder and less motor power). In addition, only one person in the feeding section is sufficient for operating the machine. -
5. High quality, uniformed sized round shaped pellets
The die-face pelletizing system can efficiently produce high-quality PP and PE pellets that are ideal for extrusion and injection. The water ring pelletizer does not create waste as it does with the spaghetti-type pelletizer.
Overview of POLYSTAR's Integrated Plastic Recycling System
- No pre-cutting required: The cutter-compactor design is ideal for light-weight material (film and film flakes)
- One-stage extruder alone can handle highly printed film: Less material degradation, energy and space-saving compared to traditional plastic recycling systems
- Improved filtration and degassing units can handle highly printed material
- Self-adjusting pelletizing speed for higher quality and more uniform-sized pellets
- A more compact design with a higher output
- Improved die-face pelletizing system for PP, BOPP, and OPP film/woven/raffia waste
Filtration and Degassing
- A continuous filter with two flowing channels reduces operator intervention.
- The double-degassing and high-vacuum can effectively process highly printed and humid material
- The re-positioning of the filter and degassing eliminates the problem of material leaking in the vent (degassing) area in conventional plastic recycling systems. This allows producers to achieve higher production and process printed film more efficiently
Application
Examples
Good degassing and filtration are probably the most important processes in pelletizing machines when it comes to post-consumer recycling. On many occasions, a two-stage recycling pelletizing machine is preferred by professional recyclers who focus on post-consumer recycling.
The washed material is fed into the compactor for a quick densifying process (which at the same time further dries the material by natural heat and friction); this helps to stabilize the material feeding into the extruder. The material then goes into the first (main) extruder for the filtration process and a two-vented degassing (installed with a high-efficiency vacuum system). The material then passes through an open area for the third and final degassing and enters the second stage (short) extruder where the second filtering process is done.