We use cookies and other tracking technologies to improve your browsing experience on our website, By clicking "Accept All," you agree to allow cookies to be placed to enhance your browsing experience on this website to show you personalized content and targeted ads, to analyze our website traffic, and to understand where our visitors are coming from. You can manage your cookie settings below. Clicking "Confirm" indicates your agreement to adopt the current settings.
Three Layer ABA Blown Film Machine
Advantages of ABA Multilayer Blown Film Machine
ABA multilayer blown film machine produces 30% stronger film
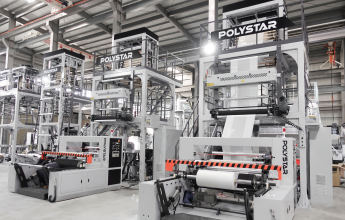
Two Extruders, Three Layers
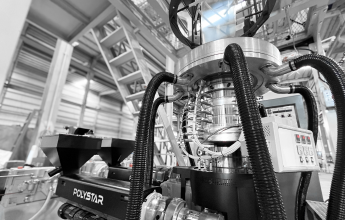
Enhanced Film Durability, 30% Stronger Than Monolayer Flim
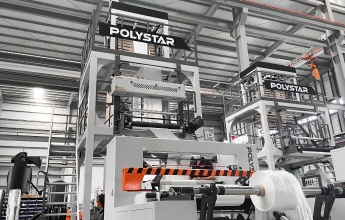
World-leading Multilayer Blown Film Machine Manufacturer
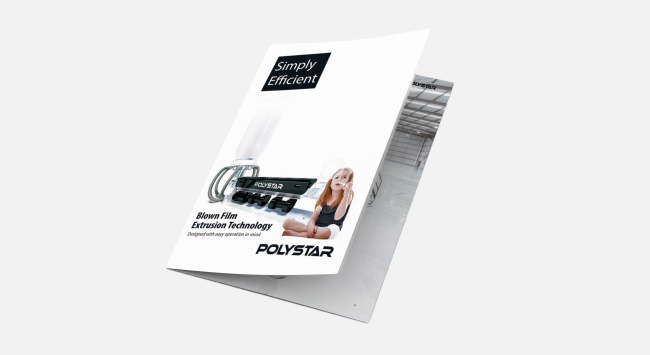
Blown Film Machines Catalog
-
T-shirt Bags
-
Bottom-sealed flat bags
-
Shopping bags
-
Supermarket Bags
-
Garbage bags
-
Table Covers/ Sufra rolls