We use cookies and other tracking technologies to improve your browsing experience on our website, By clicking "Accept All," you agree to allow cookies to be placed to enhance your browsing experience on this website to show you personalized content and targeted ads, to analyze our website traffic, and to understand where our visitors are coming from. You can manage your cookie settings below. Clicking "Confirm" indicates your agreement to adopt the current settings.
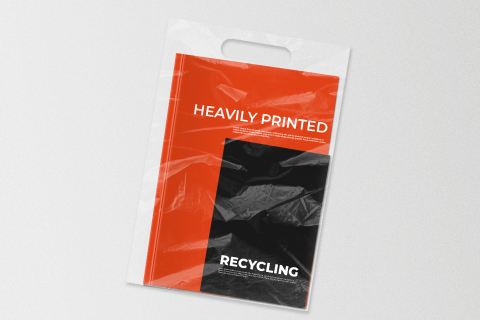
Heavily Printed PE/PP Film Recycling
The recycling process of highly printed films requires pelletizing machines with specialized degassing systems depending on the percentage of printed surface on the film in order to ensure quality pellets.
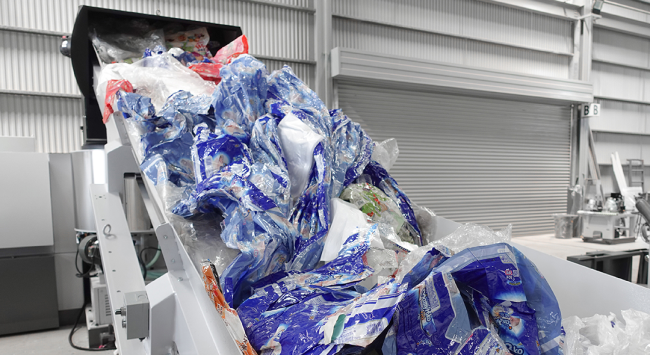