We use cookies and other tracking technologies to improve your browsing experience on our website, By clicking "Accept All," you agree to allow cookies to be placed to enhance your browsing experience on this website to show you personalized content and targeted ads, to analyze our website traffic, and to understand where our visitors are coming from. You can manage your cookie settings below. Clicking "Confirm" indicates your agreement to adopt the current settings.
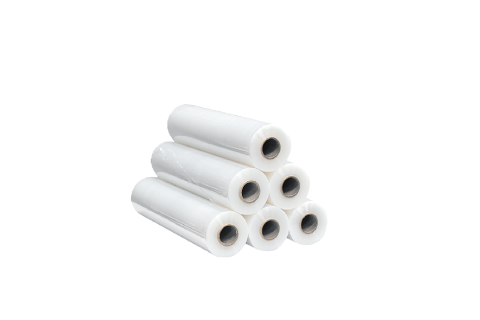
Stretch Film Recycling
Recycling this material helps decrease its environmental impact.
How to Recycle Stretch Film Wrap Materials?
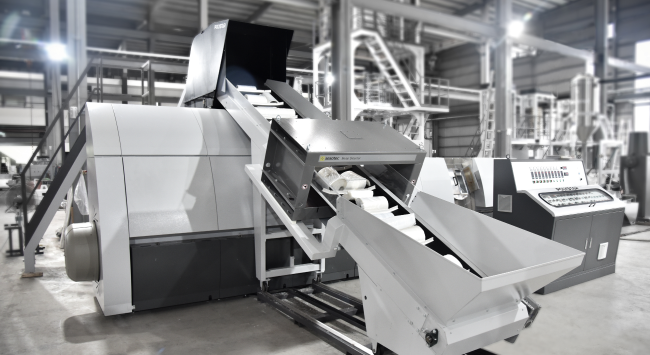
Optimize your stretch film / cling film recycling with POLYSTAR's shredder-integrated recycling machine. These materials often include adhesives for enhanced performance, posing recycling challenges. Our innovative recycling solution is engineered to overcome these obstacles, streamlining and enhancing the recycling process.
Our stretch film recycling machine incorporates a single-shaft shredder, allowing you to feed rolls through a nip roller or load entire rolls of stretch film (without paper core) directly into the machine's feeding band. Resulting in an efficient recycling process for recovering LLDPE/LDPE materials.