We use cookies and other tracking technologies to improve your browsing experience on our website, By clicking "Accept All," you agree to allow cookies to be placed to enhance your browsing experience on this website to show you personalized content and targeted ads, to analyze our website traffic, and to understand where our visitors are coming from. You can manage your cookie settings below. Clicking "Confirm" indicates your agreement to adopt the current settings.
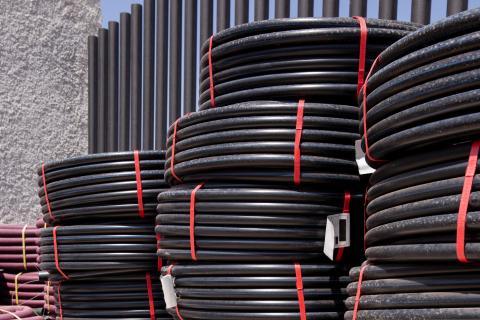
Drip Tape Recycling
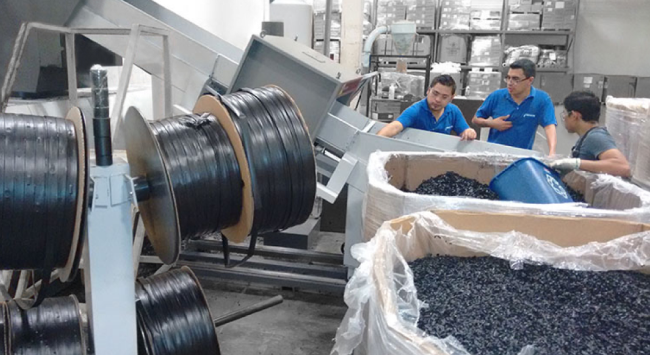
How to Recycle Drip Tape?
POLYSTAR’s high-efficiency, one-step plastic recycling machine Repro-Flex is designed for the reprocessing plastic drip tape, soft irrigation tape, PE polyethylene (HDPE, LDPE, LLDPE), and PP polypropylene flexible packaging material.
This cutter-integrated pelletizing system eliminates the need for pre-cutting the materials and requires less space and energy consumption while producing high-quality plastic pellets at a productive rate.
The Advantages of Using Repro-Flex Drip Tape Recycling Machine
-
Special Design for Recycling Irrigation Pipes
Repro-Flex plastic pelletizer is designed for recycling LDPE or HDPE drip tape or soft irrigation pipes. This pelletizer has the built-in cutter compactor that can be used to cut and compact drip tape, making the recycling process easier and more effective. -
Extruding + Pelletizing
After the drip tape is preconditioned, it directly enters the extruder at a continuous pace. Then the material gets transferred to the pelletizing unit (Hot die face pelletizer), where the plastic pellets are produced. Resulting in a much higher production output compared to other recycling systems on the market. -
Higher Pellets Quality
Thanks to these advantages, the output pellets can still maintain the material properties, allowing producers to add recycled drip tape plastic pellets directly into their production lines.