We use cookies and other tracking technologies to improve your browsing experience on our website, By clicking "Accept All," you agree to allow cookies to be placed to enhance your browsing experience on this website to show you personalized content and targeted ads, to analyze our website traffic, and to understand where our visitors are coming from. You can manage your cookie settings below. Clicking "Confirm" indicates your agreement to adopt the current settings.
Bag Production. Double the Efficiency.
Monolayer Blown Film Machine
Normally when producing film rolls for T-shirt bag conversion which ranges from 300~700mm in width, it is difficult to achieve higher output by using a bigger extruder for such a small film width unless the blown film extruder is equipped with an internal bubble cooling. The twin-head blown film machine offers an economic alternative and has a much faster return on investment compared to a blown film machine installed with an internal bubble cooling system (IBC). In the twin-head blown film machines, 1 die head can reach much higher output with a bigger extruder (such as 65mm or 75mm in diameter) even when producing smaller width film. It is especially effective for T-shirt bag makers who are looking for a machine with higher output but lower cost. Compared to extruders with a single die head, the twin die extruders can achieve higher production capacity when producing film rolls that are small in width, as the high extrusion output is dispersed into two separate channels of the die heads instead of one.
POLYSTAR designs and customizes this type of twin-head blown film machine with different screw diameters and roller widths depending on the customers’ requirements. Available in screw diameters of 55mm, 60mm, 65mm, and 75mm and film width from 400mm up to 1000mm on each winder. The double-head blown film machine also allows producers to switch between HDPE and LDPE production as well as produce different film widths on the same machine on each winder simultaneously. A special screw design is used to provide good mixing and stable output for both HDPE and LDPE materials. Bimetallic treatment is applied to process a higher percentage of recycled material and CaCO3 compound. POLYSTAR uses Siemens/ABB energy-saving motors for the extruders which can reduce energy consumption by up to 5%. POLYSTAR has installed more than 200 sets of double-head blown film machines in Latin American in more than 15 countries throughout Central and South America.
Higher production for thin film and small-sized bags
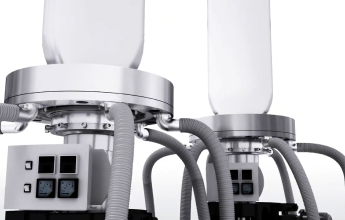
Designed for HDPE and LDPE Bag Producers
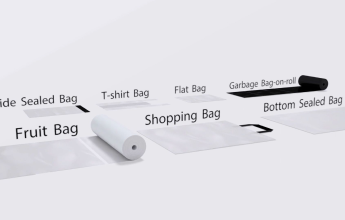
Productive for All sizes.Flexible in production.
The ability to produce different film widths and thicknesses on each winder at the same time also adds flexibility to the production.
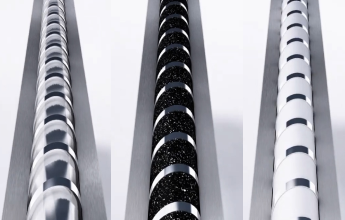
Works with Different Materials. Recycled, Virgin, CaCO3, Biodegradable.
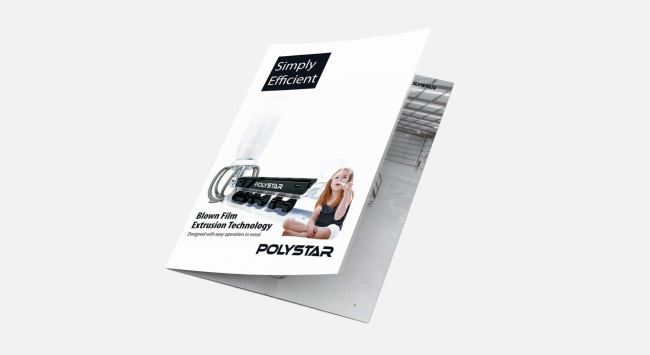
Duo-X Catalog
-
Side Sealed Bag
-
T-shirt Bag
-
Garbage Bag-on-roll
-
Fruit Bag
-
Shopping Bag
-
Bottom Sealed Bag