We use cookies and other tracking technologies to improve your browsing experience on our website, By clicking "Accept All," you agree to allow cookies to be placed to enhance your browsing experience on this website to show you personalized content and targeted ads, to analyze our website traffic, and to understand where our visitors are coming from. You can manage your cookie settings below. Clicking "Confirm" indicates your agreement to adopt the current settings.
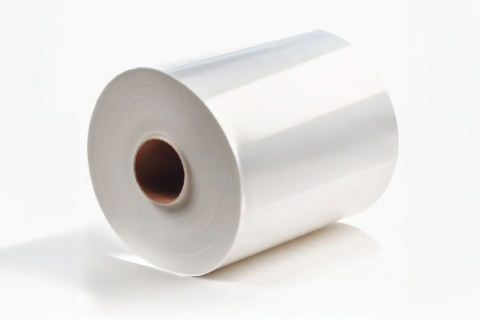
BOPP Film Recycling
It offers product protection and presentation in packaging, provides secure sealing and bonding in various applications, showcases graphics and visuals in printing, enhances the visual appeal and durability in various processes, decorates floral arrangements, adds aesthetics to gift wrapping, enhances tamper-evident features in security documents, and helps protect / cover products.
High-Performance Recycling Machine for BOPP Film
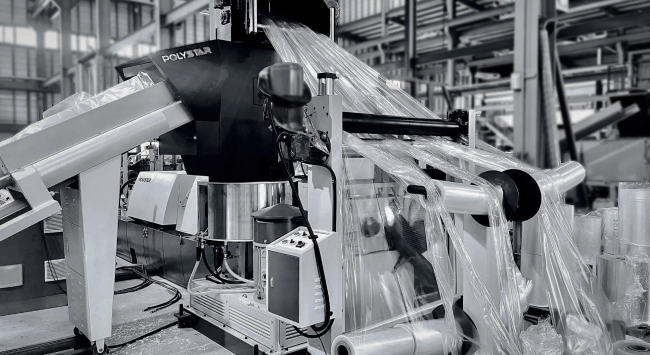
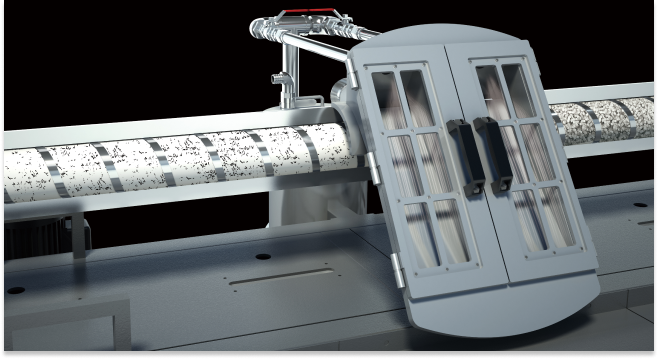
Degassing
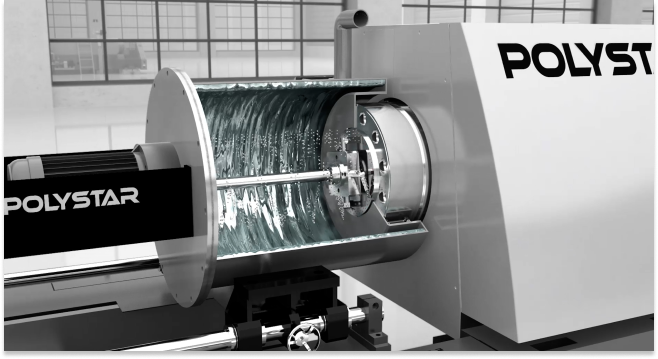