We use cookies and other tracking technologies to improve your browsing experience on our website, By clicking "Accept All," you agree to allow cookies to be placed to enhance your browsing experience on this website to show you personalized content and targeted ads, to analyze our website traffic, and to understand where our visitors are coming from. You can manage your cookie settings below. Clicking "Confirm" indicates your agreement to adopt the current settings.
An Opportunity in Kenya's Plastic Recycling Market
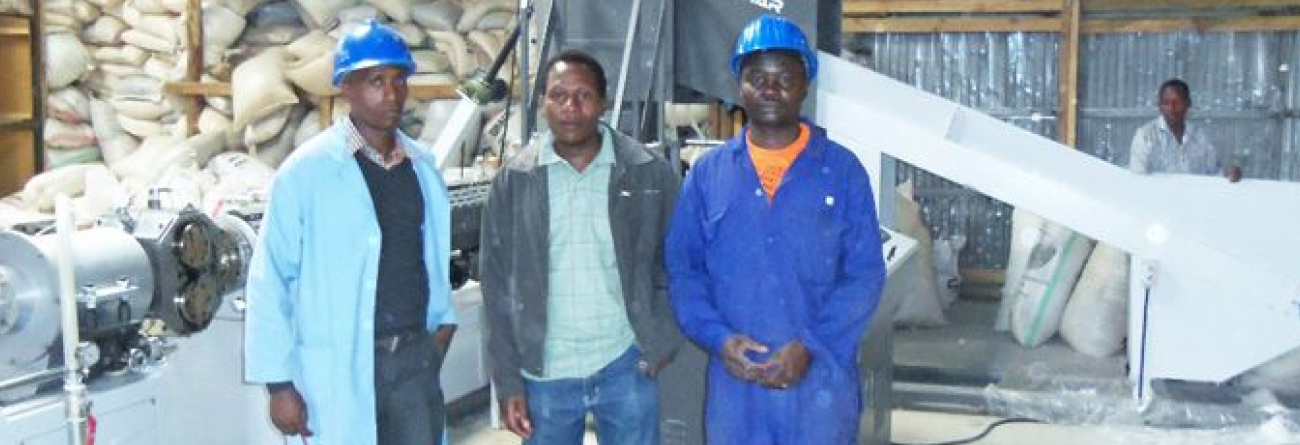
Diverse Productions and Applications in Kenya
POLYSTAR Machinery Co., Ltd, a leading Taiwan manufacturer of plastics processing machinery, has recently installed a set of cutter-integrated plastic film recycling machines in Kenya. The film producer is based in Nairobi, and it supplies primarily shrink film, shrink bags/ sleeves, stretch films, and PE sheets. The company produces and distributes plastic packaging products and offers solutions to various food processing industries such as dairy, tea, and coffee.
All-in-one Direct Recycling
POLYSTAR's high-efficiency, one-step plastic recycling machine HNT-V is designed for the reprocessing of PE polyethylene (HDPE, LDPE, LLDPE) and polypropylene (PP) flexible packaging material, printed and non-printed. This cutter-integrated pelletizing system eliminates the need for pre-cutting the material and requires less space and energy consumption whilst producing high-quality plastic pellets at a productive rate.
In addition to in-house (post-industrial) film waste, the system is also able to process washed flakes, scraps, and regrind (pre-crushed rigid plastic waste from injection and extrusion). This equipment is highly recommended for packaging film producers of commercial bags, garbage bags, agricultural films, food packaging, shrink and stretch films, as well as producers in the woven industry of PP woven bags, jumbo bags, tapes, and yarns. Other types of materials such as PS sheets, PE and PS foam, PE net, EVA, and PP mixed with PU are also applicable to this machine.
Special Design of POLYSTAR Plastic Recycling Machine
1. Machine Units
2. Ideal Solutions for the Film Producers
The integration of the cutter compactor and extruder ensures extremely fast and stable feeding, the tangentially connected extruder is continuously filled with pre-compacted material. This results in a much higher production output compared to other types of recycling systems on the market.
The stable material feeding together with the hot die face pelletizer produces round-shaped, uniformed-size pellets that are higher in value and optimal for reproduction (extrusion processes).
The unit is ideal for blown and cast film producers where the leftover waste of edge trim from the blown film in the format of scraps (T-shirt bags cut-offs from bag making and punching processes), complete film rolls and sheets can be efficiently recycled in a simple process. The high-quality, uniformed-sized recycled pellets are almost like virgin material that can be put directly back into the film production line.
For PP woven and raffia producers, the in-house waste generated from the production of PP woven bags, non-woven, jumbo bags, PP raffia, PP woven sacks, and tapes can be used. The recycled PP pellets can be reused (100%) for production in most cases, such as in circular weaving looms and tapelines.
Demanding other Machines
Kenya has seen a growing demand for advanced technologies to serve booming industries. In particular, the plastics industry demands processing and recycling machines that are highly efficient, cost-saving, and flexible, requirements that are being met by Taiwan-based POLYSTAR Machinery Co., Ltd