We use cookies and other tracking technologies to improve your browsing experience on our website, By clicking "Accept All," you agree to allow cookies to be placed to enhance your browsing experience on this website to show you personalized content and targeted ads, to analyze our website traffic, and to understand where our visitors are coming from. You can manage your cookie settings below. Clicking "Confirm" indicates your agreement to adopt the current settings.
Is Plastic Foam Recyclable? EPP, EPS, EPE Foam Recycling
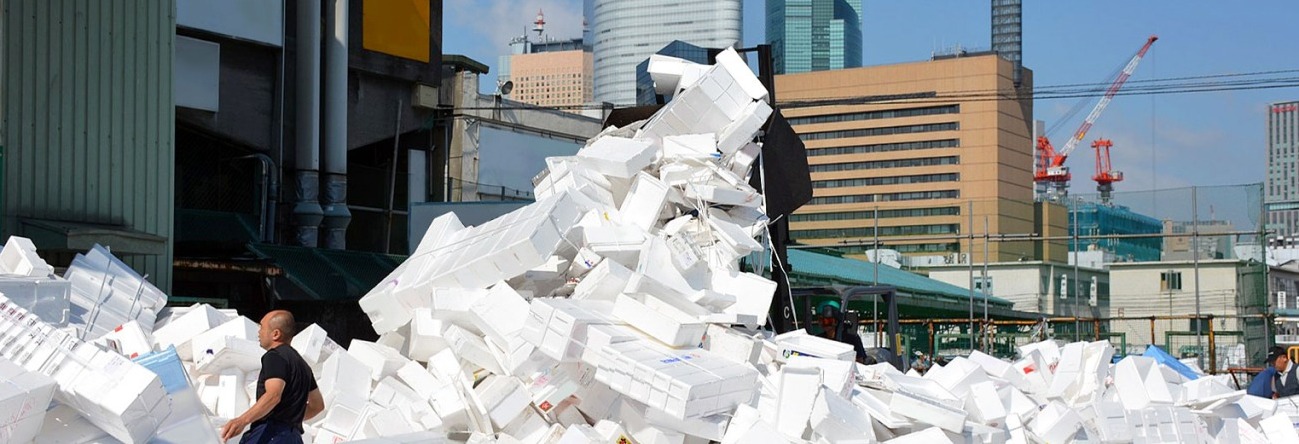
Plastic foam materials are often used in many different daily life applications including packaging, logistics, construction, food and beverage packaging, and stationery applications.
These wide usages of plastic foams also bring the question of whether the foams are recyclable. The short answer is yes, most of the foams such as EPE, EPP, and EPS foams are technically recyclable.
What are the types of plastic foams that are recyclable?
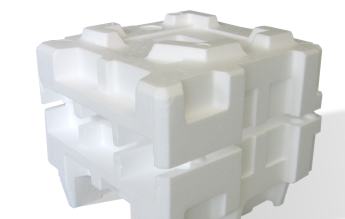
1. EPS foam recycling
- EPS foam recycling machine installed in Saudi Arabia - Customer stories
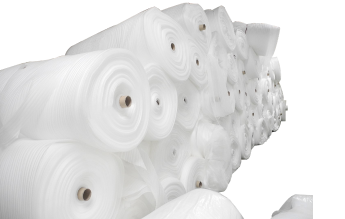
2. PE foam (EPE foam) recycling
PE foams are often used for the packaging of fragile goods as well as for heavy goods, electronic products, tools, and machinery. We can also see PE foams in the applications such as floating pool noodles, floor underlays, shock absorbers, sports equipment, and so on.
EPE foam recycling machine installed in Germany - Customer stories
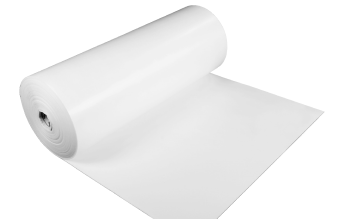
3. PP foam (EPP foam) recycling
Polypropylene foams, also known as expanded polypropylene (EPP) are famous for their rigid yet flexible structure, flexibility for low and high temperature, and moisture and chemical resistant characteristics. That makes PP foams very convenient to use in applications where durability and lower mass are needed. Therefore, we often see PP foams or EPP in cushioning, heavy-duty packaging, automotive components, thermal, and sound insulation applications.Recommended machines for EPS, EPP, EPE foam recycling
1. Repro-Flex cutter-compactor plastic recycling machine
POLYSTAR’s Repro-Flex cutter compactor integrated plastic recycling machine provides a one-step recycling experience since cutting, extrusion and pelletizing processes can be done in this machine. The built-in cutter-compactor cuts the materials into small pieces, pre-heats them with frictional heat, and prepares the extrusion materials.
Repro-Flex ensures the feeding consistency of the plastic materials during the entire recycling process. As the first step, materials are fed to the cutter-compacter via an auto-controlled belt conveyor, which automatically adjusts the feeding speed based on how full the cutter compactor is. From the cutter-compactor, materials are directly fed into the recycling extruder stably with centrifugal force.
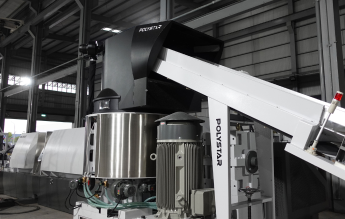
2. Repro-One shredder integrated recycling machine
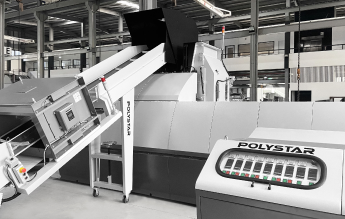
Thanks to the direct connection of the shredder to the recycling extruder, the plastic materials are fed into the extruder easily. After the extrusion and pelletizing steps, the uniform and high-quality pellets with minimal degradation can back to the production lines or be traded in the market.
We have briefly mentioned the general specifications of two POLYSTAR plastic granulator machines that are suitable for foam recycling. On the other hand, plastic foams are varied in terms of material types, expansion rates, sizes, and shapes. To find your customized plastic granulator machine for foam recycling, please contact POLYSTAR and we will help you find a simple solution.
About the Author
Resul Gökpınar
International SalesResul creates up-to-date content based on his experience, gained by solving customers' problems in Turkey and the EMEA market.