We use cookies and other tracking technologies to improve your browsing experience on our website, By clicking "Accept All," you agree to allow cookies to be placed to enhance your browsing experience on this website to show you personalized content and targeted ads, to analyze our website traffic, and to understand where our visitors are coming from. You can manage your cookie settings below. Clicking "Confirm" indicates your agreement to adopt the current settings.
How to Produce a Good-quality LDPE Shrink Film?
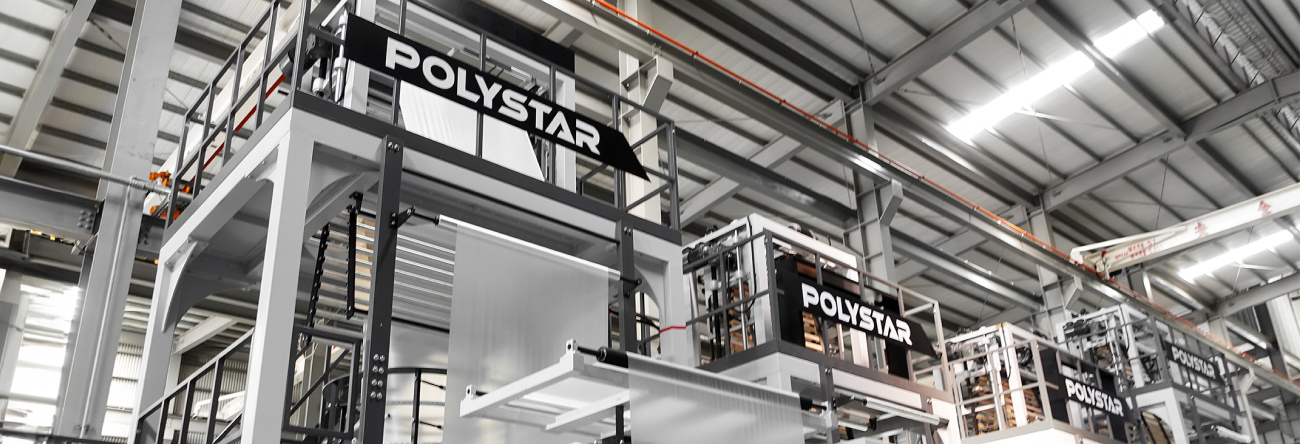
Shrink film is widely used around the world, it helps pack products more conveniently. This makes it possible to pack larger quantities of products and deliver more products at a time, and it reduces shipping costs for the suppliers.
Shrink film can be made of several types of materials. The most common ones on the market today are polyvinyl chloride (PVC), polyolefin (POF), and polyethylene (PE).
As for PE, there are 3 different forms which include Low-Density Polyethylene (LDPE), Linear Low-Density Polyethylene (LLDPE), and High-Density Polyethylene (HDPE).
For shrink film application, LDPE would be the best choice, as it has higher strength and more durability for heavier items.
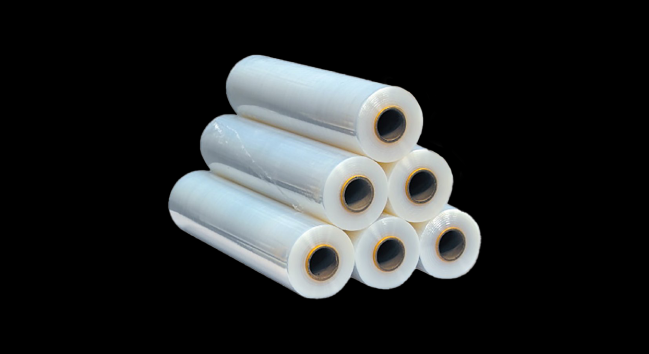
Key Benefits of LDPE Shrink Film
LDPE shrink film is also printable and can have excellent graphics added while still maintaining the image and the strength required. It also does not have many of the drawbacks of alternative shrink-wrap materials such as PVC and POF.
Therefore, using LDPE to produce shrink film is one of the most popular ways among shrink film producers today.
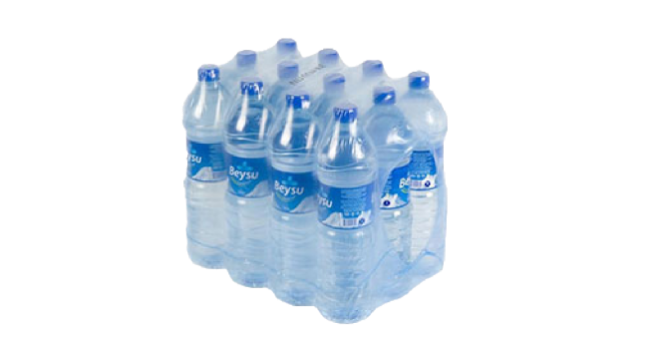
Further advantages of LDPE shrink films:
- Good visibility of the film, making it easy to recognize the product inside.
- Protecting the environment since LDPE shrink film is 100% recyclable.
- LDPE film can easily be blended with various chemical additives or other film materials to enhance the original properties.
What machine do you need to produce a good-quality LDPE shrink film?
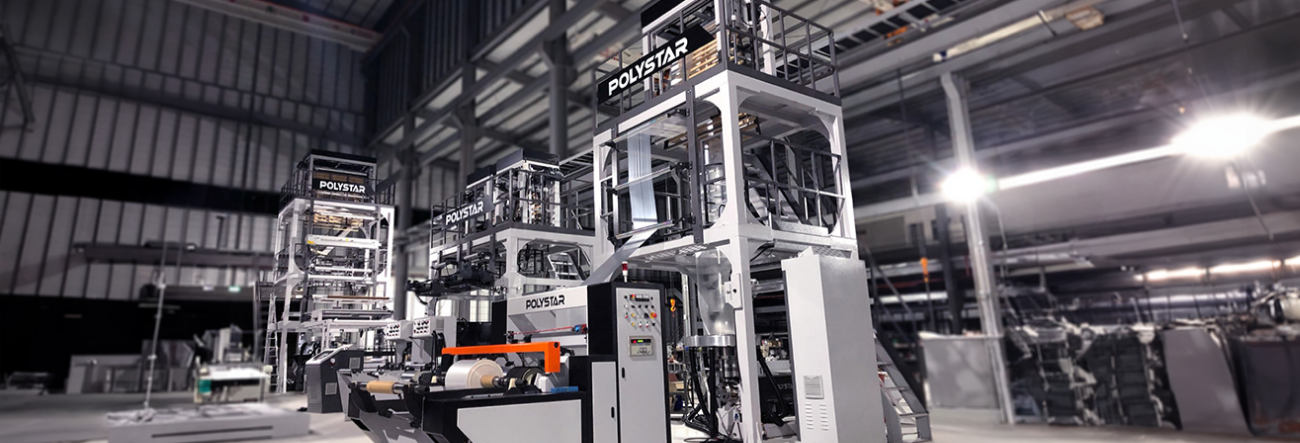
This machine has been one of our best-selling models in the last 20 years, and it has earned recognition for its outstanding performance and stability. Our customers are using this model to produce high-end shrink film and earn profits even in highly competitive markets.
POLYSTAR has set a new standard in the industry thanks to our excellent design of the extruders, which can produce the film with the best quality and have better thickness control.
This specially designed blown film extruder has a good ability for melting and mixing the material with different formulas. The high-precision die head and cooling air ring give the shrink film outstanding thickness control and resistance.
Essential optional devices for producing high-quality LDPE shrink film
To ensure the quality of your LDPE shrink film, the following optional devices are required during the production:
Are you ready to start LDPE shrink film production?
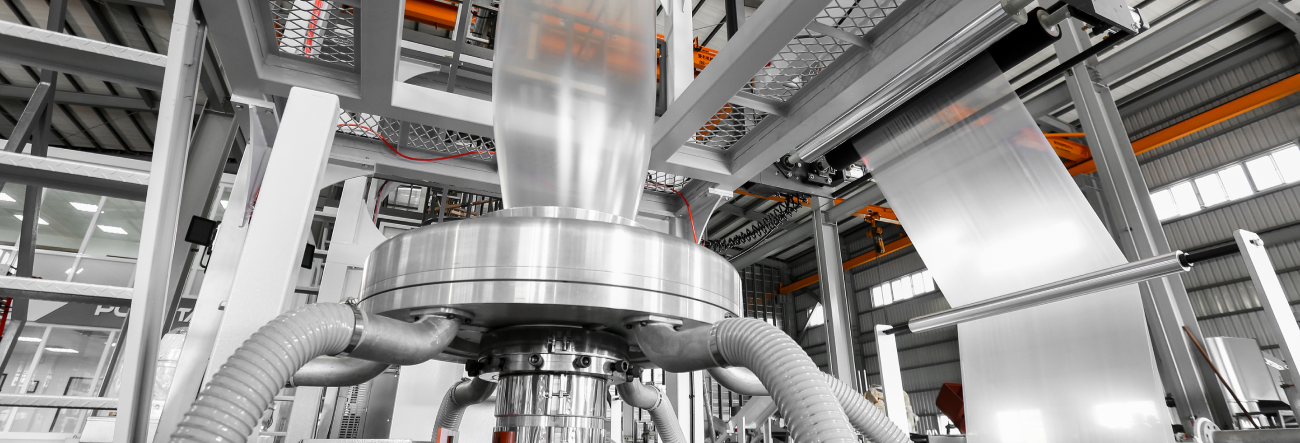
POLYSTAR has a professional and responsive sales team to assist you in choosing your blown film machine for producing LDPE shrink film. On certain models, we also offer fast delivery so you can get started on your production straight immediately.
All the blown film machines manufactured by POLYSTAR are simple in operation, which means they are extremely user-friendly even for operators without experience.
Easy operation and maintenance are the reasons why POLYSTAR is so popular in the market today. Are you ready to start your LDPE shrink film business? POLYSTAR is here to offer you the best solution.
About the Author
Derek Shiao
Derek Shiao is a business development manager at POLYSTAR. He keeps up with the latest trend in the plastic industry and creates content based on his experience offering various solutions to customers.