We use cookies and other tracking technologies to improve your browsing experience on our website, By clicking "Accept All," you agree to allow cookies to be placed to enhance your browsing experience on this website to show you personalized content and targeted ads, to analyze our website traffic, and to understand where our visitors are coming from. You can manage your cookie settings below. Clicking "Confirm" indicates your agreement to adopt the current settings.
300th Shredder - Plastic Recycling Machine goes to India
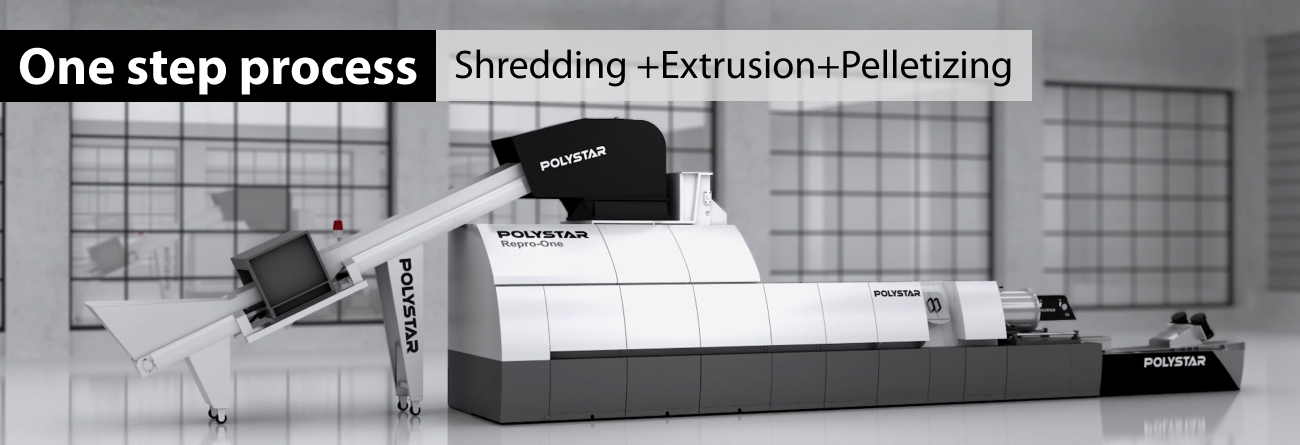
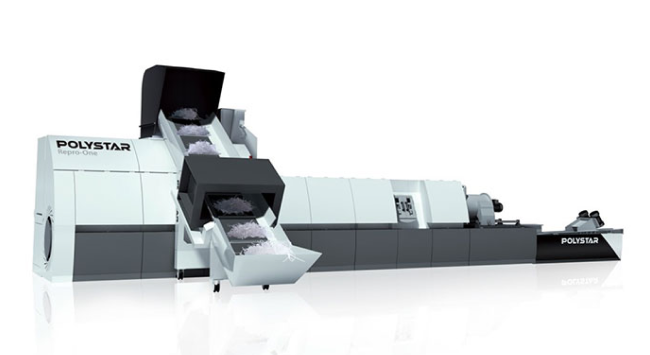
Machine number 300: An increasing demand for raffia and woven recycling worldwide
Amongst these 300 worldwide installations of this machine model, 75 machines are installed in states of Gujarat, Kolkata, Bangalore, and Raipur, India, where the demand for higher quality recycling machines is increasing, particularly for PP raffia, FIBC, woven sacks, and HDPE non-woven in-house waste.
The recycling machine has a heavy-duty shredder built-in, which is designed specifically to turn different forms of production waste generated during the woven bag-making process (extruder start-up lumps, winding, weaving, bag making, and printing) back into high-quality recycled pellets which can be reused again in tape extrusion lines.
This special machine design with a single-shaft shredder integrated allows woven bag producers to handle this difficult-to-process material in one step at higher efficiency and lower cost.
Machine # 5 for the Indian raffia and woven producer
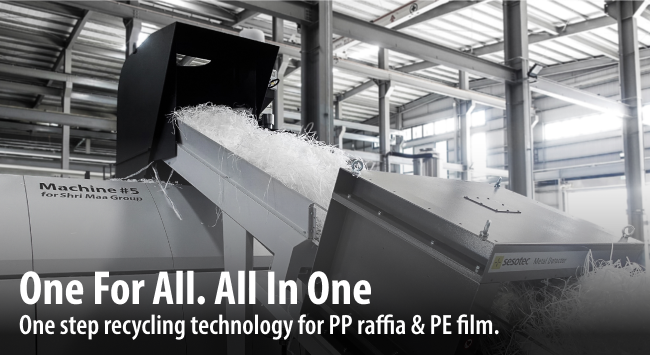
“We also recommended the machine to our friends in the industry who produce mosquito and construction net, and they are very happy using the machine as well.”
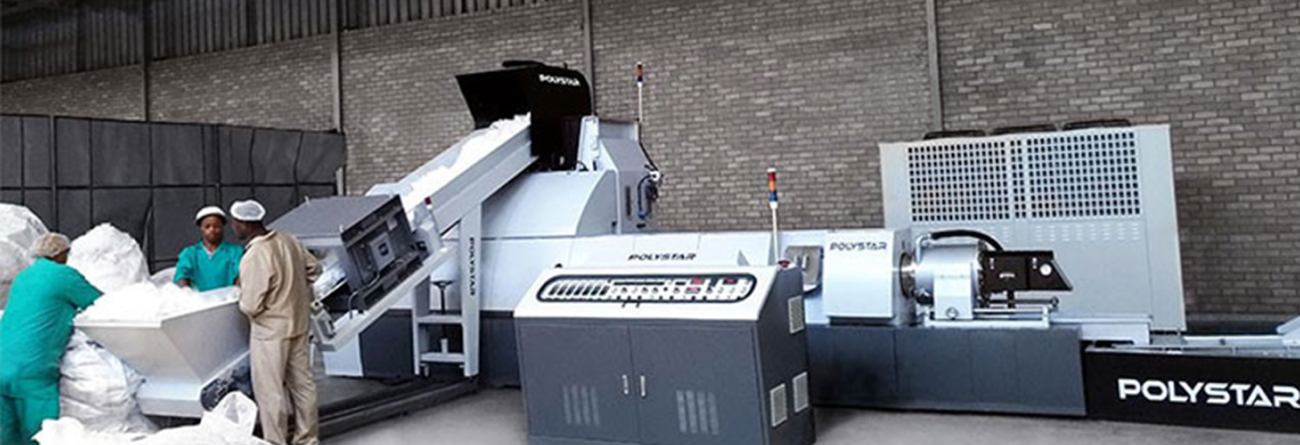
The high-quality pellets ensure easy reuse back again in the production process for raffia, non-woven, and Ad*Star block bottom heavily printed bags. The reusability of the PP recycled pellets is particularly high with the Repro-One recycling machines, raffia producers can use between 20% to 100% recycled pellets back into the production line depending on the final product requirement.
Powerful yet gentle – A new combination
What makes the Repro-One special is that the built-in shredder is capable of processing material with high strength such as pp raffia, tapes, filaments, fabrics, and lumps directly without the need to pre-crush.
The system is different from the recycling machine with a rotating-cutter/cutter compactor built-in, which is used mainly for recycling lightweight material such as plastic film and bags.
The combination of
- Powerful shredder to process raffia and woven in one step
- Low processing temperature in the shredder
- Smart feeding control to prevent overloading and underloading makes this machine the perfect recycling solution for PP woven bag producers.
Higher pellets reusability.
Lower production cost.
In the case of a woven sack producer who used to recycle using off-line shredders and agglomerators before feeding the material into the extruder. Ever since having installed the Repro-One 100, the producer has reduced the operation cost by 30%.
__23L12dQy8f.png)
“Our PP sack recycling process was divided into several steps with separate machines before, consisting of Grinder → Agglomerator → Extruder → Pelletizer → Dryer. We wanted to find a better way for recycling sacks and woven polypropylene bags.”
According to Suresh Sharma, Director of Operation of the producer based in Kenya.
According to Suresh Sharma, Director of Operation of the producer based in Kenya.
After getting good references from other companies who recycle PP sacks, FIBC, bulk bags and jumbo bags using POLYSTAR, the company decided to invest in the first Repro-One plastic pelletizing machine in 2016.
“We’ve found the right recycling solution with POLYSTAR, now that everything is done in one single step” he added. “I have to say that the process is better in almost every aspect – recycled pellets with higher reusability, less labor required, less electricity cost, and the design of the machine makes the recycling process smooth and continuous.”
The ideal recycling solution for PP woven bag producers worldwide
In the Repro-One machine, the waste material is fed without pre-cutting into the plastic crusher by a conveyor belt. A hydraulic “pusher” presses the material against the rotor where the material is shredded and cut in between at a low processing temperature. After shredding, the material is fed directly into the extruder for further filtration and degassing before pelletizing.
__23L12kRE1g.png)
The combination of shredder, extruder, and pelletizer into one machine is the ideal solution for raffia and woven bag producers who need to process their internal waste, as the powerful (shredder) yet gentle (low processing temperature) process produce the best possible pellets quality at the lowest operation cost.
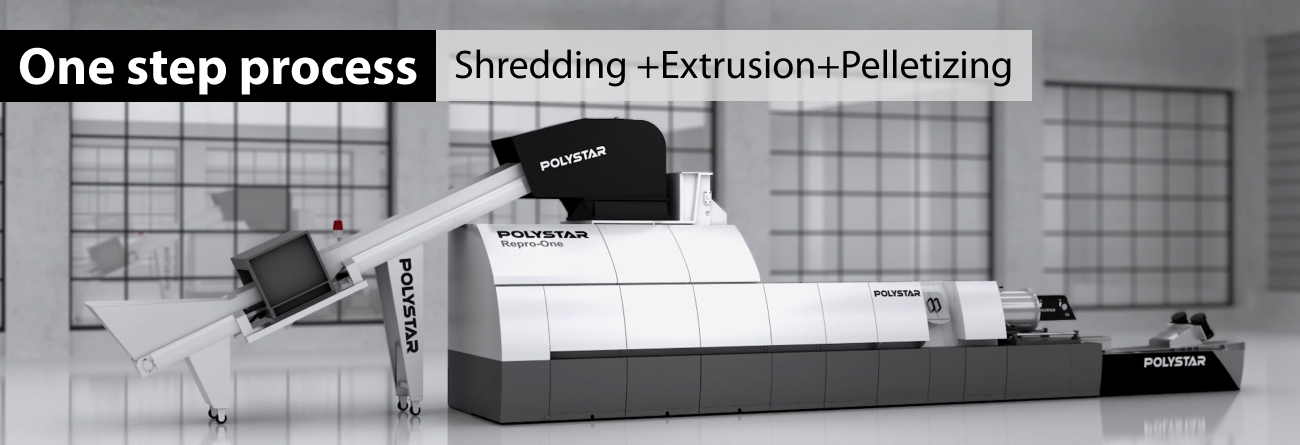
Many PP raffia and woven bag producers have already seen the great benefits of doing in-house recycling using the Repro-One, including producers in Argentina, Azerbaijan, Congo, Ethiopia, India, Indonesia, Mexico, Myanmar, Philippines, Saudi Arabia, Sudan, Swaziland, Thailand, Turkey, Kenya, Kuwait, USA, and many others.
About the Author
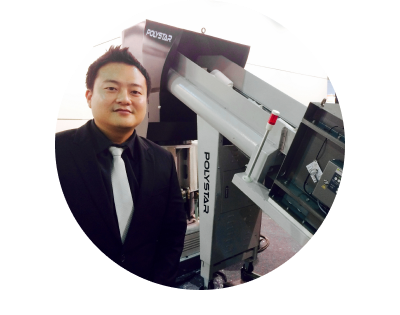
Jack Lin
Sales ManagerJack has visited and spoken to hundreds of POLYSTAR machine users around the world over the last 10 years. Having collected practical information on customer feedback and user experiences, he enjoys sharing the advantages and disadvantages of using different types of machines with others, especially coming from the customers' perspectives.